A Comprehensive Guide to the Process and Benefits of Plastic Extrusion
In the substantial realm of production, plastic extrusion arises as a highly reliable and vital procedure. Translating raw plastic right into continual accounts, it caters to a huge selection of industries with its remarkable versatility.
Understanding the Basics of Plastic Extrusion
While it may appear complex at first glimpse, the procedure of plastic extrusion is essentially basic - plastic extrusion. It is a high-volume production method in which raw plastic is melted and shaped into a constant account. The process starts with the feeding of plastic material, in the form of powders, granules, or pellets, into a warmed barrel. The plastic is then thawed making use of a mix of heat and shear, used by a revolving screw. When the molten plastic reaches completion of the barrel, it is forced with a small opening referred to as a die, forming it right into a desired type. The shaped plastic is after that cooled, solidified, and cut into desired lengths, finishing the process.
The Technical Process of Plastic Extrusion Explained
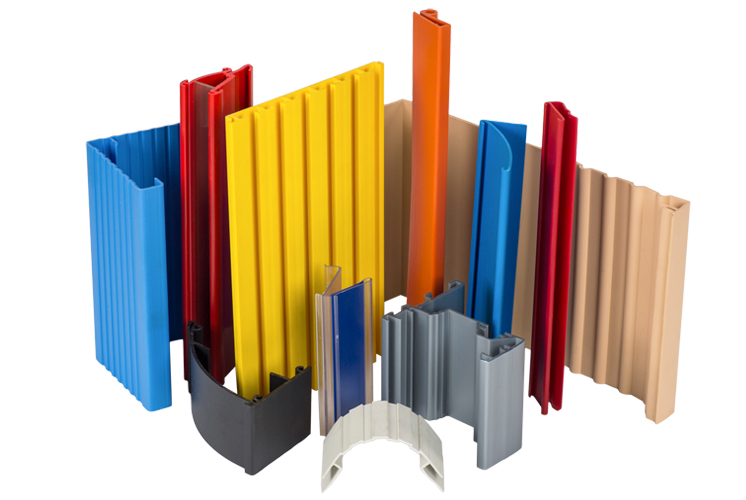
Kinds of Plastic Suitable for Extrusion
The option of the right kind of plastic is a vital aspect of the extrusion procedure. Various plastics use unique residential properties, making them much more suited to specific applications. Recognizing these plastic types can significantly boost the extrusion procedure.
Comparing Plastic Extrusion to Other Plastic Forming Methods
Understanding the types of plastic suitable for extrusion leads the way for a wider conversation on how plastic extrusion piles up against various other plastic forming approaches. Plastic extrusion is unmatched when it comes to producing continual profiles, such as gaskets, pipes, and seals. It also allows for a regular cross-section along the length of the item.
Secret Benefits of Plastic Extrusion in Production
In the realm of production, plastic extrusion offers numerous considerable advantages. One noteworthy benefit is the cost-effectiveness of the procedure, that makes it an economically enticing production technique. Additionally, this strategy gives superior product flexibility and improved manufacturing rate, consequently increasing total manufacturing efficiency.
Cost-efficient Manufacturing Technique
Plastic extrusion leaps to the center as a cost-effective manufacturing approach in manufacturing. This process sticks out for its ability to generate high quantities of product swiftly and efficiently, supplying suppliers with substantial cost savings. The primary cost benefit is the capacity to use cheaper basic materials. Extrusion uses thermoplastic products, which are less expensive contrasted to porcelains or steels. Additionally, the extrusion procedure itself is fairly easy, reducing labor costs. Additionally, plastic extrusion needs less energy than standard production techniques, adding to reduced functional prices. The procedure likewise reduces waste, as any kind of malfunctioning or excess materials can be reused and recycled, providing another layer of cost-effectiveness. Generally, learn the facts here now the monetary advantages make plastic extrusion an extremely appealing choice in the manufacturing market.

Superior Product Versatility
Beyond the cost-effectiveness of plastic extrusion, another considerable benefit in producing lies in its superior product adaptability. This makes plastic extrusion a perfect service for markets that need customized plastic elements, such as automobile, construction, and packaging. In essence, plastic extrusion's item adaptability promotes advancement while boosting operational performance.
Enhanced Manufacturing Rate
A considerable benefit of plastic extrusion exists in its improved production speed. This production process permits high-volume production in a reasonably brief time period. It is capable of creating long, continuous plastic profiles, which substantially reduces the production time. This high-speed manufacturing is especially beneficial in sectors where large quantities of plastic components are required within limited due dates. Couple of other manufacturing processes can match the rate of plastic extrusion. Furthermore, the ability to preserve constant high-speed manufacturing without compromising item top quality establishes plastic extrusion besides various other techniques. The improved production rate, consequently, not just enables manufacturers to satisfy high-demand orders however likewise adds to raised performance and cost-effectiveness. This helpful feature of plastic extrusion has made it a preferred option in numerous industries.
Real-world Applications and Influences of Plastic Extrusion
In the realm of production, the strategy of plastic extrusion holds extensive significance. This procedure is commonly utilized in find out the manufacturing of a variety of items, such as plastic tubing, window frames, and climate removing. Therefore, it significantly affects fields like building and construction, packaging, and automotive industries. In addition, its effect prolongs to daily things, from plastic bags to tooth brushes and non reusable cutlery. The financial benefit of plastic extrusion, largely its economical and high-volume result, has reinvented manufacturing. The environmental effect of plastic waste continues to be a worry. Consequently, the market is persistently making every effort for technologies in biodegradable and recyclable products, indicating a future where the advantages of plastic extrusion can be preserved without jeopardizing environmental sustainability.
Final thought
In conclusion, plastic extrusion is a reliable and very effective approach of transforming basic materials right into diverse products. It offers many advantages over various other plastic creating approaches, including cost-effectiveness, high outcome, marginal waste, and layout versatility. Its influence is exceptionally really felt in numerous industries such as building, vehicle, and durable goods, making it an essential procedure in today's manufacturing landscape.
Digging deeper into the technological process of plastic extrusion, it begins with the selection of visit site the suitable plastic product. When cooled down, the plastic is reduced into the called for sizes or injury onto reels if the item is a plastic movie or sheet - plastic extrusion. Contrasting Plastic Extrusion to Various Other Plastic Forming Approaches
Understanding the types of plastic ideal for extrusion leads the method for a more comprehensive discussion on how plastic extrusion piles up versus various other plastic creating approaches. Few other manufacturing processes can match the speed of plastic extrusion.
Comments on “Plastic extrusion for optimized, scalable manufacturing solutions”